The best of ancient and modern: renovating a 17th century Shropshire home
Nick Cowern and his partner Margaret Martin want the world to know that heat-pumps work well – even in houses built 400 years ago
The story we often hear about heat-pumps is that they work in well insulated modern homes but aren’t so good in older houses.
Well, Professor Nick Cowern and Margaret Martin beg to differ, and they’re keen to tell heat-pump sceptics all about how their beautiful 17th century Shropshire home is kept toasty warm by their new air-source heat-pump.
But that’s just one element of a labour-of-love restoration journey that has seen them get to grips with a whole host of sustainable building materials, old and new…
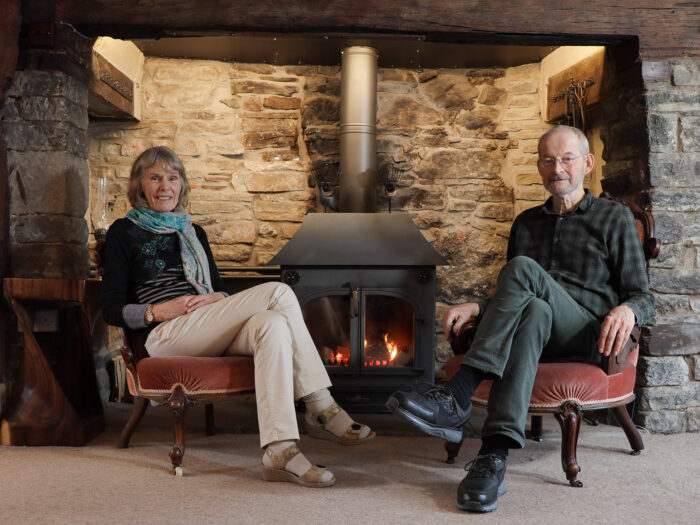
Margaret and Nick in front of their inglenook fireplace
Nick and Margaret bought their four-bed, 220m2 ancient farmhouse in 2022.
>According to its Grade-II listing, it dates from the 17th Century, though the couple believe parts could be older still.
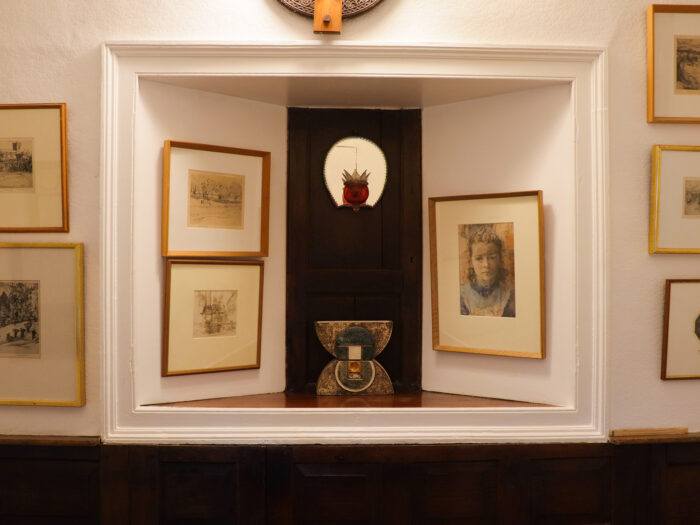
The panelled entrance hall contains an alcove that may have originally been a wig cupboard. The etchings and pastel portrait are by Nick’s late father, artist RT Cowern RA
The oldest part of the house is timber-framed, with a lovely inglenook fireplace and huge, wonderful beams that look as if they have been reused.
Margaret says, “I think a lot of the timbers came from ships.”
The slightly later, stone-built end of the house is three storeys tall, with a cellar.
Throughout, there are all the characterful features you could wish for, including wonderful wood panelling reputed to have come from the village church, plus, some tasteful modern additions such as oak French doors, and a balcony off the master bedroom.
Shropshire Hills
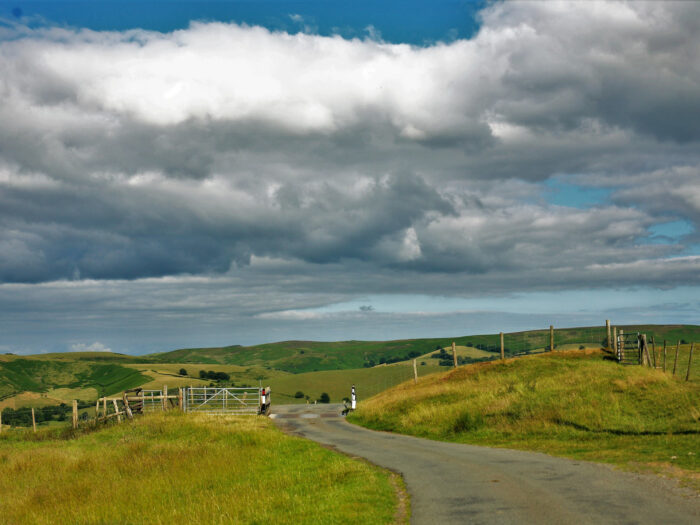
The couple live in a remote corner of beautiful Shropshire Image credit: Jeanne Menjoulet under Creative Commons
The house lies a few miles north west of Ludlow, in a deeply rural area amid the rolling Shropshire Hills, just near the Welsh border.
Poet A E Housman, famous for A Shropshire Lad, wrote another poem about this beautiful part of the world that begins with the lines:
‘Clunton and Clunbury,
Clungunford and Clun,
Are the quietest places
Under the sun.’
New life in Shropshire
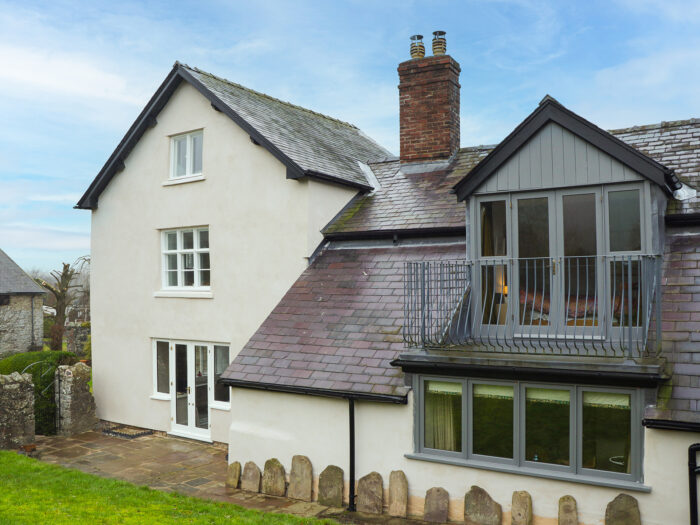
The old house looks wonderful after its renovation
Nick and Margaret moved to this bucolic spot from North Yorkshire where they both lived to begin a new life together as a couple.
Margaret, who had done many things during a varied career, from conference interpreting to management consultancy, had sadly lost her husband.
She then met retired physics professor Nick, whose family had connections in Shropshire and a great love for the area.
Deciding it was time for a new start in a new place, they considered various options for their relocation before settling on Shropshire.
“We looked for ages and couldn’t find what we wanted and then we found this place.
“We wanted a large garden, and we wanted to be in a village.
“And this has it all. We bought it, knowing that we’d have to do a lot of work, because we were just in love with it,” Margaret says.
Ancient house
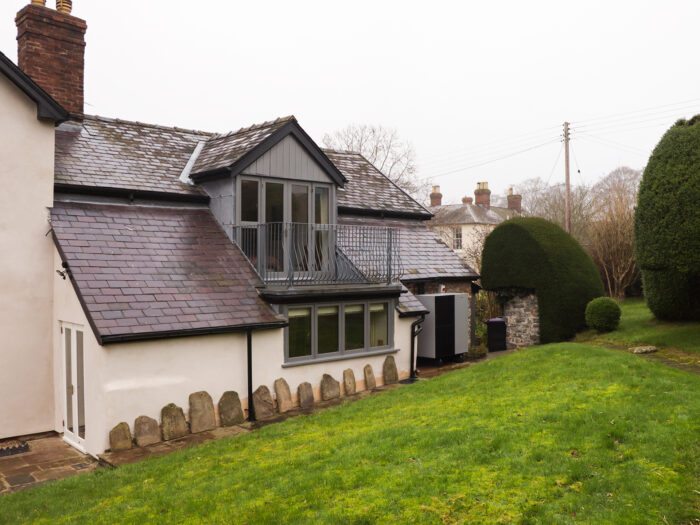
The master bedroom has a balcony overlooking the garden
Nick says, “We don’t know quite when it was built. Various clues lead us to think the oldest parts could even have been built in the 1500s.
“The wood panelling is reputed to have come from the church at the time of Oliver Cromwell in the mid 17th Century.
“But the way it is installed suggests the house was already quite old and sagging a bit at that point.”
Sustainable lifestyle
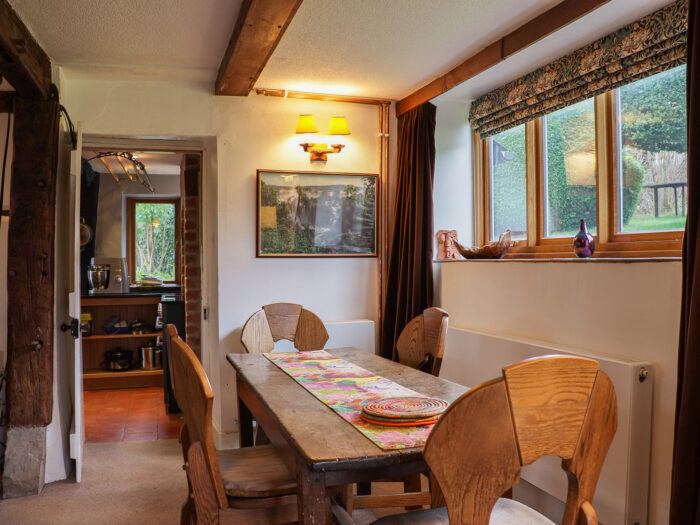
The dining room with its oak table is in the house’s former dairy – one of the new, flat-panelled radiators sits behind the table and chairs
The couple are passionate environmentalists, and were determined that whatever work they undertook on the house should be done using sustainable materials and would reduce their energy use.
When they moved in, the house had oil-fired central heating, but with a limited number of radiators that only reached part of the house.
“We hadn’t spotted how few there were when we looked round,” says Margaret.
“There was no heating in the kitchen or either bathroom. I nearly froze that first winter.”
Structural repairs
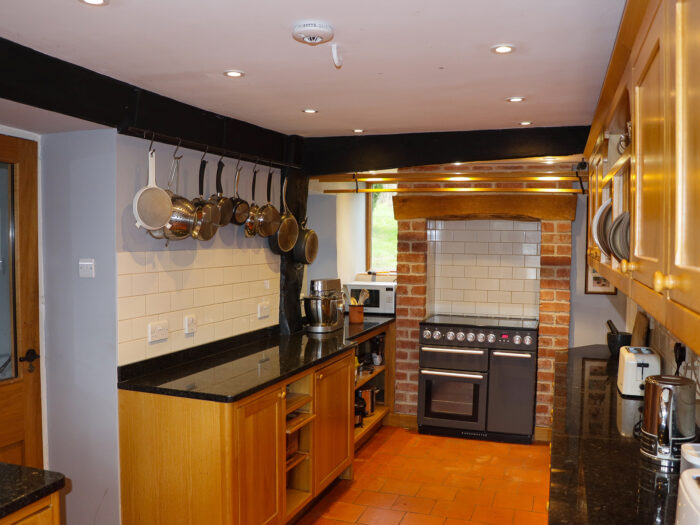
The couple have left the kitchen unchanged apart from the addition of a new radiator
But before they could think about any eco retrofits, the couple had work to do on the fabric of the building.
Cement render applied in the 1960s had wreaked havoc on the building’s stone walls.
Nick says, “One of the walls of the house was leaning outwards, the window was bowing right out.
“We thought, ‘Well, this doesn’t look terribly safe, but it’s probably been like that for hundreds of years.’
“We did think we’d better investigate though. And that was the start of it…
“The walls in the stone-built part of the house are about 60cm thick with a rubble core.
“But once we knocked a hole in one, this ‘stuff’ just slid out.”
Earth mortar
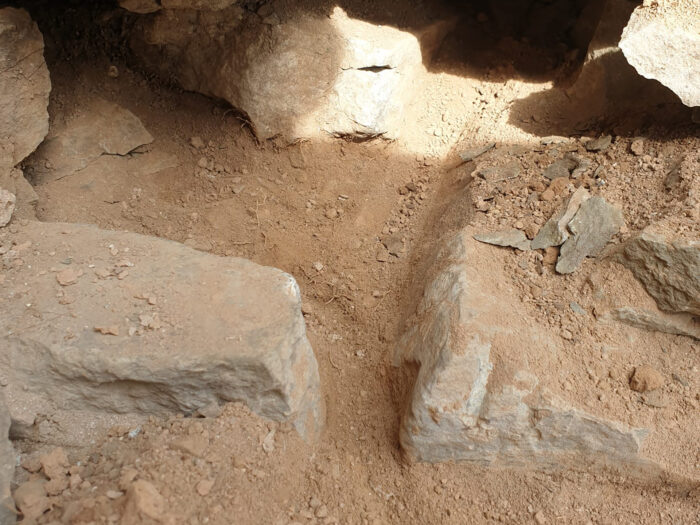
The problematic earth mortar
The ‘stuff ‘was earth mortar – local subsoil used to infill between rocks in the core of walls – a very common material in centuries past because it was easy and cheap to use.
Found, for example, in many ancient churches, its strength depended on the underlying geology.
Some types of soil made stronger mortar than others, with clay soils, in particular, making good mortar – but it also relies on the outside of the walls being protected with weatherproof lime mortar.
Earth mortars can perform well for centuries, but, if a wall containing earth gets waterlogged – perhaps because of a broken gutter, say, or because, as in this case, it has been covered with a non-breathable cement render that subsequently cracks, trapping water inside the wall – then serious problems can arise.
The earth and water form a liquid mud that runs out from between the stones, leaving what is, in effect, a dry-stone wall.
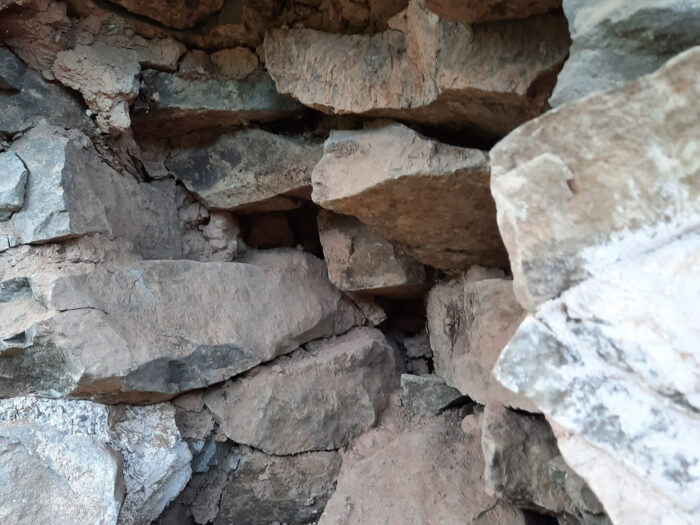
Inside the damaged stone wall of the house before it was repaired
Because it is usually hidden away inside walls, awareness of earth mortar is low, but there is increasing understanding of its value as a low-carbon building material.
There’s a useful guide to looking after and repairing buildings with clay mortars on the Earth Building UK website – and there’s some great research on the topic in a Scottish context here.
Repairing the walls
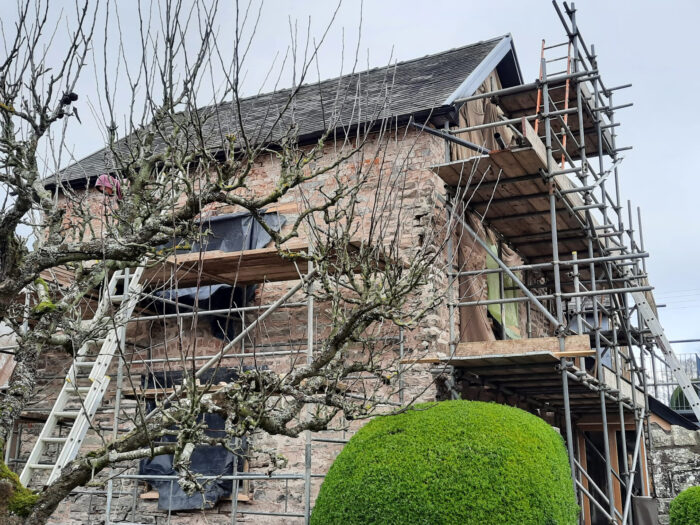
All the old cement render had to be removed from the stone walls
“Putting it right was a big job, says Nick. “By asking around locally we found some good conservation builders called PAV.
“Leo Vince and his team had to take off the cement that had caused the problems, put in new lintels, and stabilise the walls using traditional fat lime mortar.”
Margaret adds, “We found all kinds of things in the old mortar, like acorns, hazelnuts, and horsehair.”
Nick continues, “We replaced the cement render with a thermally insulating, breathable, lime-based eco plaster called Diathonite that has cork in it.
“The breathable finishing layer that goes on top comes in a range of colours and doesn’t require painting.”
Nick adds, “The Council’s Historic Environment Officer wasn’t sure about the Diathonite to start with, but now they are going to keep an eye on how it performs, with a view to recommending it for other period buildings.”
Timber frame
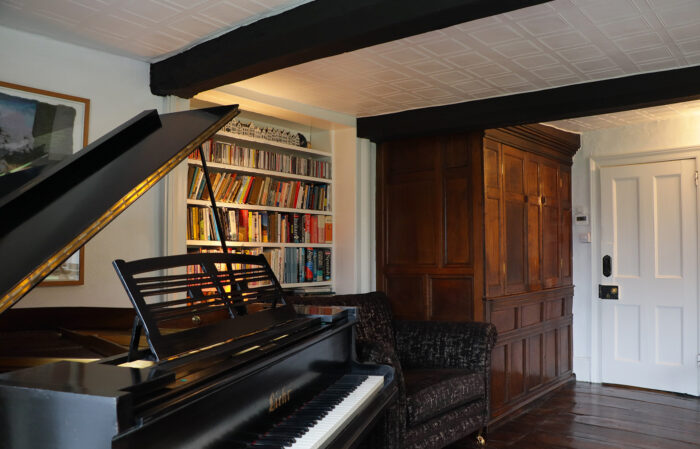
The music room contains panelling thought to have been rescued from St Swithin’s Church. The couple restored the original oak floor
As well as the stone-built section of the house, part is timber-framed with brick infill.
Nick explains, “Between the timbers originally would have been vertical staves and lath.
“Laths were introduced as a replacement for wattle and daub.
“Thin wooden laths were woven between wooden staves to make thin, rigid panels which are then covered with lime plaster.
“Some of this is still visible in our cellar. But, in most of the external walls, the wood has decayed and been replaced by bricks.
“The walls are just one brick thick though – so not great in terms of thermal insulation.”
Hemp plaster

The master bedroom has views over the hills and their large garden
They plastered these walls with lime hemp plaster to improve the insulation and filled gaps and cracks in the timbers using a traditional, natural ‘filler’ called oakum.
This is rope made from flax that is impregnated with pine tar (also known as Stockholm tar).
Smaller gaps were filled with a traditional sheep wool, sand and lime mix.
Then the timber frame was finished with lime wash to preserve the timbers and keep the wall breathable but watertight.
Secondary glazing
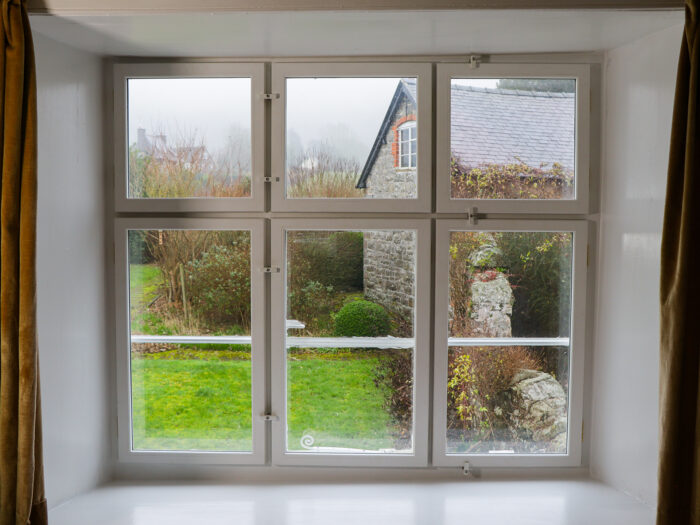
Little toggles allow the new secondary glazing to be opened
Something else that really helps prevent heat loss in the house is new secondary glazing.
Margaret says, “There was some not-very-nice secondary glazing here.
“But we asked an architect friend, Mike Overton, to design and make something better for us and what he came up with is so good.”
Nick says, “We wanted something with a minimal, slimline look to maximise the light and keep the focus on the historic windows.
“Mike’s design incorporates krypton-filled double-glazing units set into slim Accoya wood frames with bubble seals to securely close the gap to the primary windows.
“It’s fully sealed and double glazed, with very low thermal losses.
“In fact, it acts similarly to triple glazing, and keeps the house warm and cosy, while minimising running costs.”
Heat-pump
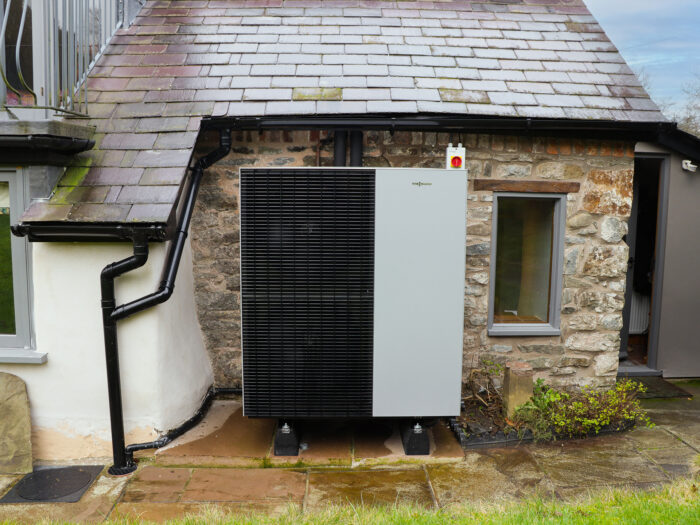
The outdoor unit of the new heat-pump tucks neatly into a corner at the back of the house where the old boiler house once stood
Once the structural issues had been resolved, Nick and Margaret updated the electrics, then it was time to tackle the heating.
They went for a heat-pump because they were determined to choose a sustainable solution, but also because the large temperature changes as a result of the old boiler’s frequent hot-cold cycling were putting stress on the building’s antique wood panelling, timbers, and furniture.
As a professional physicist, Nick was able to carry out his own heat-loss calculations based on wall temperature measurements using a thermal-imaging camera.
He also used an endoscope to look inside the internal structures of the old walls.
He says, “The measurements worked out pretty well.
“I calculated the heat loss was 10kW, and in fact it was 8kW.
“Interestingly, this is about half the heat loss that standard building U-value tables would have predicted.”
Installation
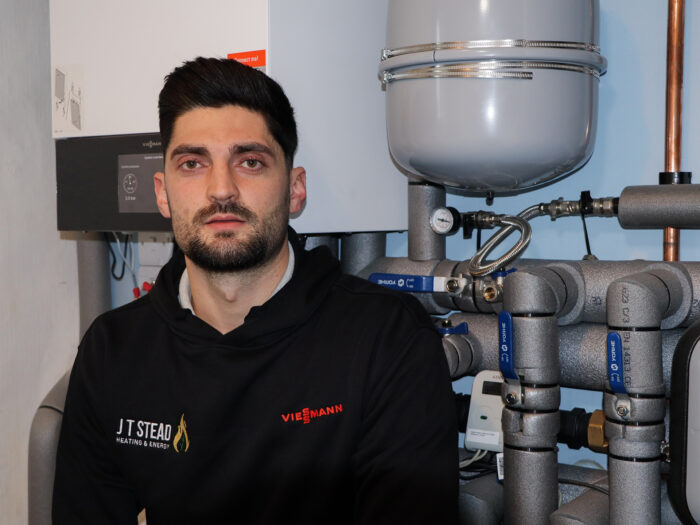
Heat-pump installer Josh Stead went the extra mile to follow the rules for a listed property
The heat-pump was installed by local engineer Josh Stead, who recommended a 16kW Viessmann Vitocal 150-A air-source heat-pump with weather compensation and 250-litre hot-water cylinder.
A compact, quiet model designed for renovation projects, the 150-A uses propane (R290) as its refrigerant, which has a low global warming potential (GWP).
Josh explains, “I like to fit heat-pumps from manufacturers with a heating background, as opposed to air conditioning, as I find they perform better.”
The house’s listed status meant heating equipment and pipe runs had to be placed out of sight, and everything had to be done without lifting original floorboards or cutting through old beams.
“Josh had to do a lot of clever pipework in tight spaces,” recalls Nick.
“There isn’t much of a gap in the loft between the chimney and the walls of the house, so he had to scramble up and squeeze into small spaces for quite a long time to do the soldering.”
One extra pipe was installed in the loft to provide extra flow capacity to the radiators on the top floor.
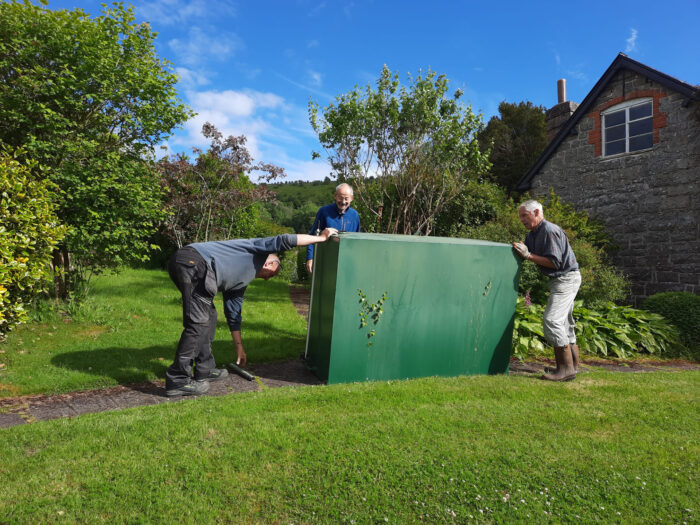
Removing the old oil tank with the help of some neighbours
The heat-pump’s outdoor unit sits in the footprint of the demolished boiler house, where it is largely invisible from outside the property, and from most of the garden.
The small indoor unit, pipework, filters, and the hot-water tank, are in wardrobe space next to the airing cupboard, which Nick and Margaret are now fitting out as a new walk-in wardrobe.
Radiators
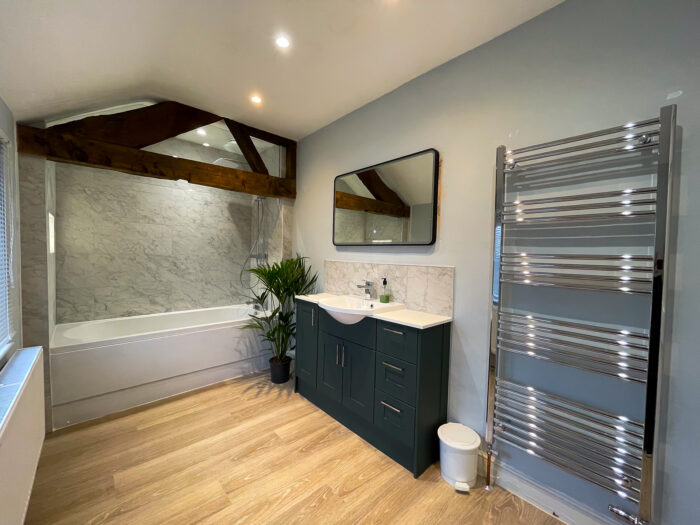
The mirror in the refurbished bathroom was positioned to give the illusion of the hidden end of the newly exposed roof truss
A grand total of 23 radiators were needed to heat the house: nine in new locations and 12 higher-output replacements for old models.
Two existing radiators were reconditioned and reused.
“We’ve got some neat little fan-assisted radiators to give good heat output where there is limited space, like in the kitchen,” says Margaret.
“And some of the nice, flat-fronted modern ones.” At -4°C outside, the system flow runs at 35-40°C.
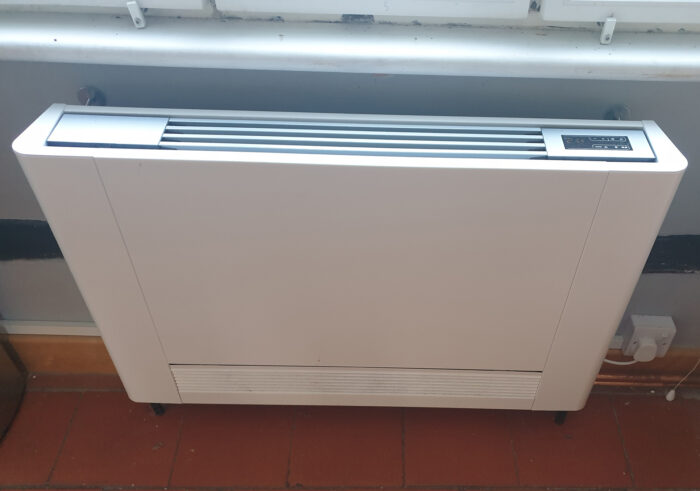
One of the new fan radiators
Good COP
Nick says, “The heat-pump is working really well.
“We’ve managed to get a coefficient of performance (COP) of about 5 out of it.”
“The coefficient of performance is a measure of how efficiently a heat-pump is working: a COP of 5 means the heat-pump is generating five times as much energy as it is using.
“For the first six months after the system was installed in July 2024, its performance data was uploaded remotely to the online heat-pump ‘charts’ at OpenEnergyMonitor.
“The system averaged a COP of 5.3, beating nearly all the other air-source heat-pumps on the site.
Nick says, “We’re very proud of that. It’s a remarkable result for a recently installed heat-pump in such an old building.”
Green fingers
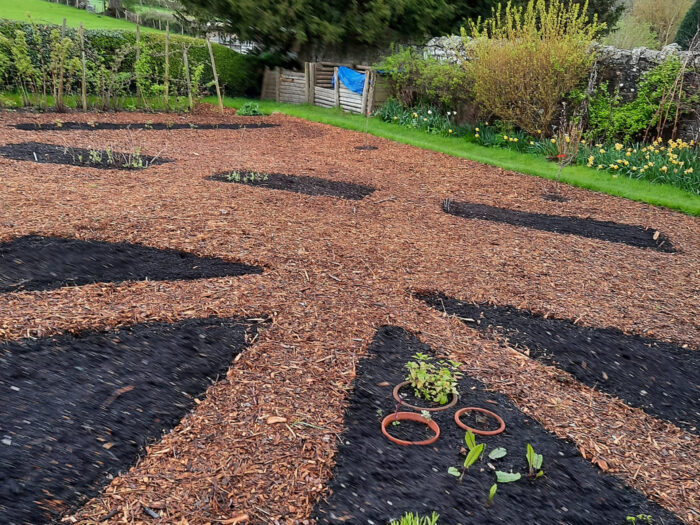
Beginning the new vegetable garden
The house came with a cottage, and a range of outbuildings including pigsties, a 17th Bentury barn and a bakehouse – complete with oven, original peel and huge bowl for kneading dough – plus a large garden.
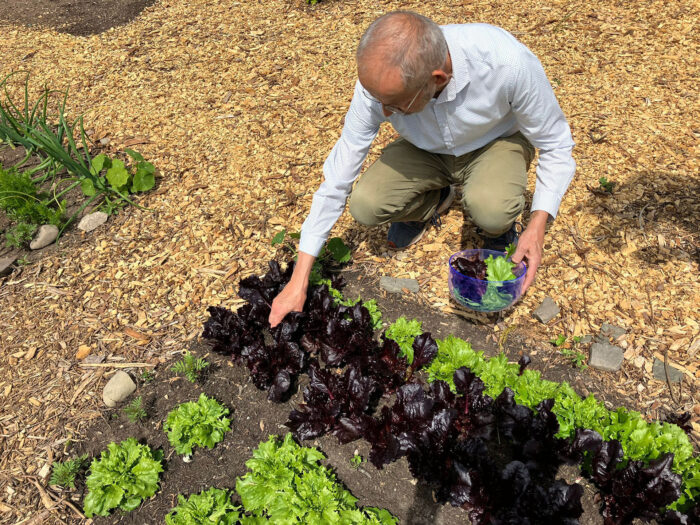
The couple love eating their own organic produce
The couple are enthusiastic gardeners and are pursuing an organic and regenerative, no-digging approach for their fruit and veg.
Nick says, “We chopped down some 7m leylandii that were blocking the light for our neighbours, and replaced them with a beech hedge.
“That meant we had a lot of woodchips to use as garden pathways and rot down as mulch.
“The soil was fairly sterile before, but now it’s full of worms and a whole range of insects, and that’s attracting so many birds and other wildlife like hedgehogs.
“Red kites fly over frequently looking for prey”
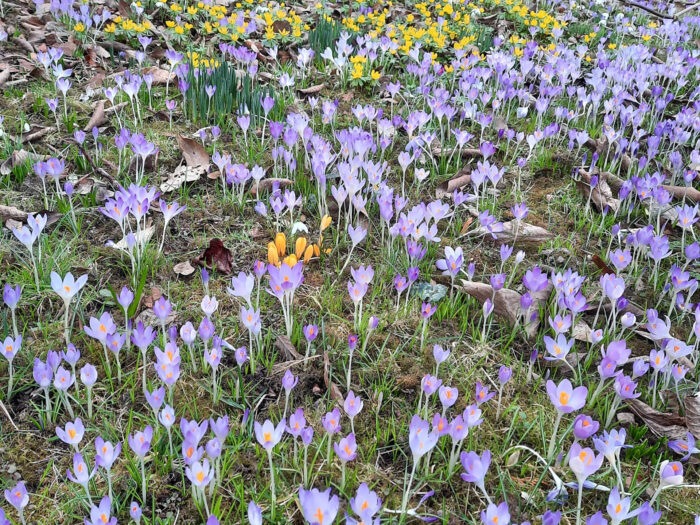
The garden with its spring carpet of crocuses and aconites was one of the big attractions of the house
Log fires
Margaret admits, “The house is lovely and warm now.
“We do still have the odd log fire sometimes even though we don’t need them, just because they are so lovely in the inglenook fireplace – and, after all, we have got 33 leylandii to get rid of…”
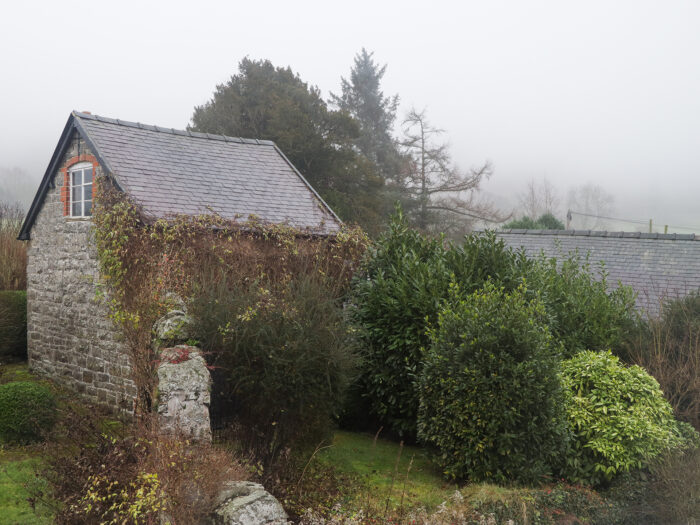
The house came with a range of outbuildings including a barn containing a cider press, a bakehouse, cottage and pigsties
READ MORE: