10 amazing modular homes
Off-site construction continues to innovate without comprising on design
Not all modular homes are the same. Some arrive on site as fully-fitted units with bathrooms and kitchens in place, while others come flat-packed and are erected in just a few days.
Whichever the chosen system, the off-site construction industry is evolving to offer products for every budget, from off-the-peg starter homes to bespoke custom-builds, using modern materials such as cross-laminated timber and including triple glazing.
1. A SIP home in Scotland
This five-bedroom modular home in North Connel, near Oban in Scotland, is a very modern take on the Highland longhouse. Designed by Scottish architect Dualchas in conjunction with Hebridean Homes, it is constructed from sound and insulation-efficient structurally insulated panels (SIPs).
The property was built for a retired couple who decided to relocate to the west coast. It offers an impressive amount of internal space, including an open-plan farmhouse kitchen and spacious living area with vaulted ceiling. To minimise wasteful corridor space, bedrooms have been placed at either end of the house.
The property, which benefits from passive solar gain, is clad in Siberian larch and took seven months to construct from start to finish.
A similar turnkey package would cost from £357,000.
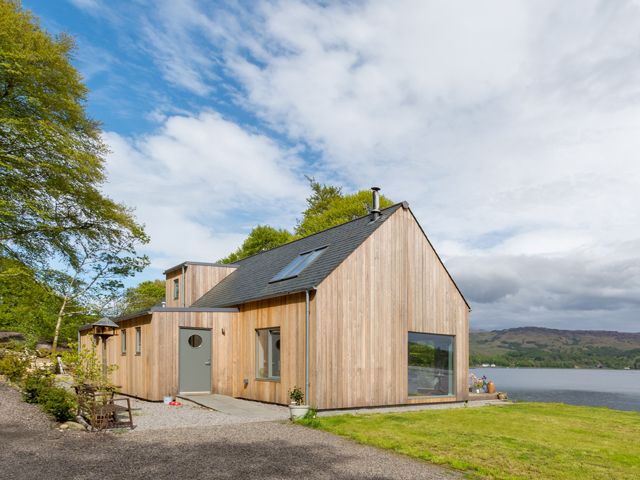
Photo: Hebridean Homes
2. A multi-purpose modular home in Norfolk
The owners of this contemporary house in Blakeney, Norfolk, wanted a place to both raise a family and use as a businesses base. The property includes an adjoining holiday-rental cabin, which is also modular, as well as a swimming pool.
The design was conceived with the input of architect Anthony Thistleton at Waugh Thistleton Architects at a build cost of less than £2,000 per square metre. This ideal modular home stands in 16 acres on the site of a 1950s house (which the couple bought and demolished) and enjoys panoramic views across Blakeney Harbour, in particular from the promontory ‘sea room’.
The property was designed to reflect the local Norfolk vernacular while making a design statement. It’s constructed from cross-laminated timber (CLT) panels, left exposed in places internally to add character and finished on the outside in napped flint and pre-weathered shiplap timber cladding.
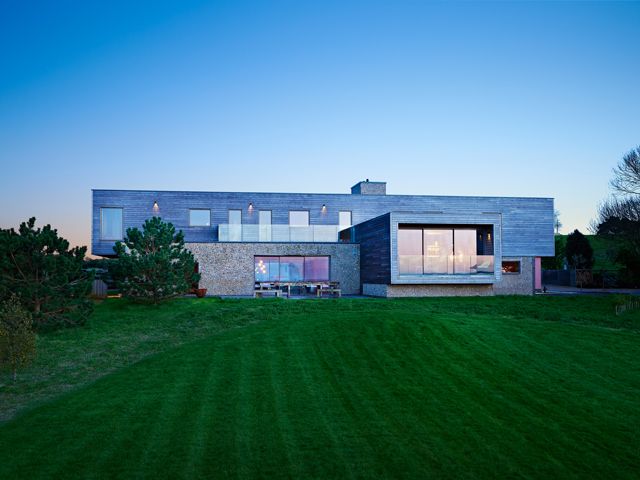
Photo: Waugh Thistleton Architects
3. A portable property on the Isle of Wight
Imagine a second home that you could pick up and take with you wherever you liked. Modular homes allows for such flexibility: although they offer the benefits of permanent construction, they can be dismantled and transported.
Retreat Homes & Lodges, in conjunction with architectural practice BuckleyGreyYeoman, created this two-bedroom house on the Isle of Wight as a second home.
It was manufactured in one piece to the BS3632 mobile park home standard, but then split into two parts for transporting and completed with a bathroom and kitchen. It’s built on a timber frame and the cladding is ThermoWood, a biodegradable thermally modified timber with insulating properties.
Similar modular homes would cost from £120,000 to include manufacture, delivery, siting and decking.
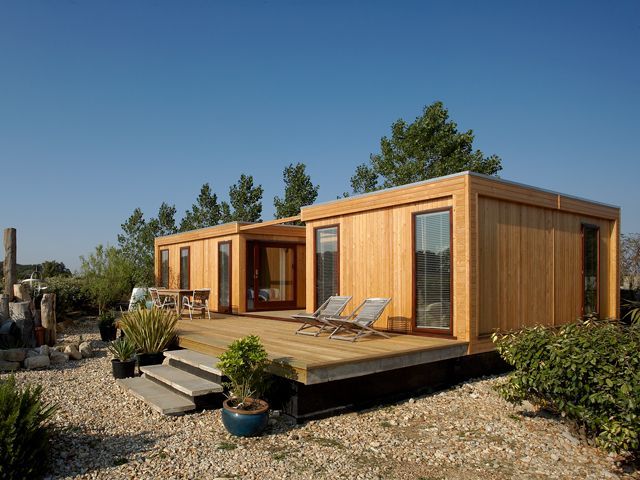
Photo: Retreat Homes & Lodges
4. A riverside home on stilts in Surrey
The above property, designed as a riverside home in Surrey for a family of four, includes floor-to-ceiling triple glazing and clerestory windows.
‘They fill this entire house with light and help to connect the rooms to each other’, says architect Peter Huf of Huf Haus.
Situated on a two-thirds of an acre plot on a bend in the river Thames, it has water on two sides. With future-proofing in mind, it is built on stilts as a precaution against flooding.
As well as for generous use of glass, Huf is known for its thermally-insulated timber post and beam structure, which removes the need for load-bearing walls and allows for open spaces.
The six metre high vaulted ceiling above the dining area looks great from the adjoining kitchen, living room and study, as well as the first-floor gallery. A similar Modum house-style project would cost from around £3,229 per square metre.
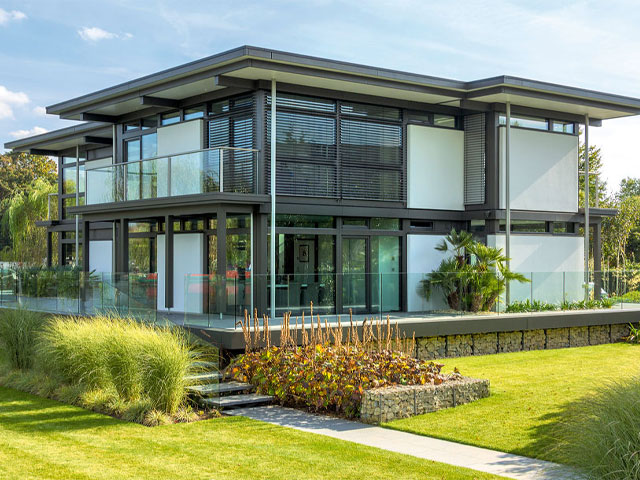
Photo: Huf Haus
5. A barn conversion in Norfolk
Modular building techniques delivered an innovative solution for this barn conversion in Shouldham, Norfolk, which links neighbouring agricultural buildings. As well as bringing two elements into one spacious home – including a cinema, games room and bar – the family also wanted to raise the height of the original barn roofs to incorporate a first floor.
This involved placing additional weight on the existing walls, so with the emphasis on conservation, carbon reduction and expediency, Swann Edwards Architecture devised a timber frame structure inside the shell of the original buildings to both support the new composite clad roof and provide a basis for the new link element between the buildings.
‘Insulated panels were then dropped inside the timber framework,’ explains homeowner Shaun Carter.
Bricks and cedar cladding on the front of the property reflect the local style seen elsewhere in the village. The total build cost was around £500,000.
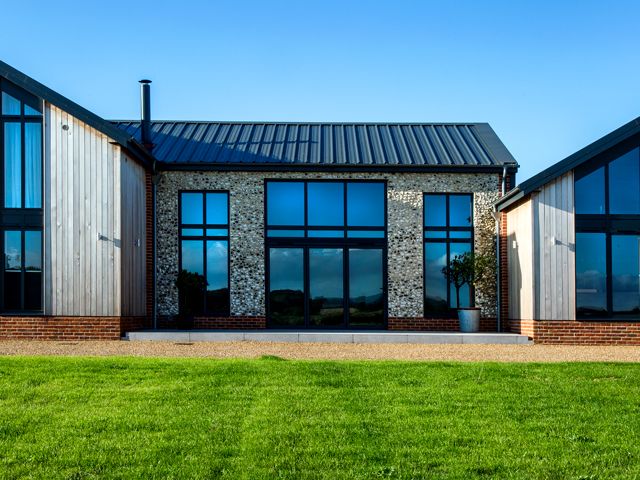
Photo: Swann Edwards Architecture
6. An adaptable Dan-Wood house in Oxfordshire
The owners of this house at the pioneering self-build and custom-build site Graven Hill, near Bicester, Oxfordshire, wanted a forever home. With this in mind, they took a Dan-Wood house type, Park 182E, and added a flat-roof annexe extension to increase the ground-floor space. It includes a kitchenette and wet room that could be used as a granny flat or office in the future.
The home, which has also been used as a show house to demonstrate the flexibility of the Dan-Wood system, is constructed from closed insulated wall panels.
It took three days to erect and seven and a half weeks to finish, and uses an air source heat pump, underfloor heating and solar panels.
The house cost £267,050, excluding the plot.
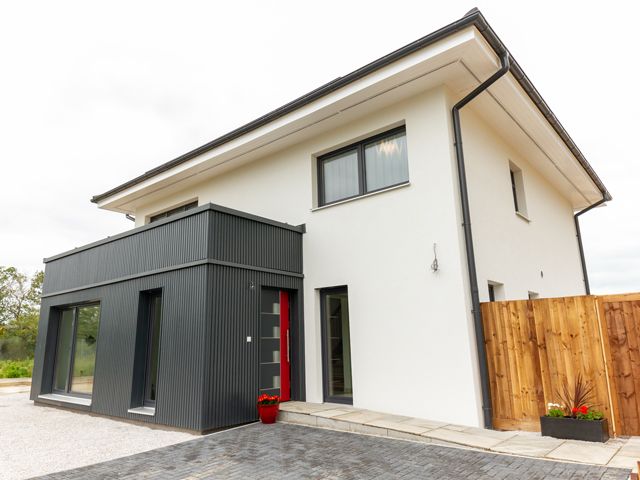
Photo: Dan-Wood
7. An energy-efficient Baufritz by the Baltic Sea
Every single window in this pristine family home opens to the Baltic Sea (the plot was part of a former naval base in Flensberg, Germany). It was designed by modular homes specialist Baufritz and based on a timber-frame construction, incorporating huge areas of energy-efficient triple-glazed glass.
Architect Maret Riemer said that the design follows a health and energy-efficiency plan, using sustainable and climate-friendly building and insulation materials. This includes a 37cm thick permeable complete wall system, comprising wood from renewable sources and natural gypsum, which offers thermal insulation and protection from electromagnetic radiation.
On the ground-floor, there is an open-plan living, dining and kitchen area, plus two bedrooms and bathrooms, while a spiral staircase leads to the first floor and the main bedroom and en-suite bathroom. The owner says his house is ‘like a rock standing in the surf’.
The cost was £507,000.
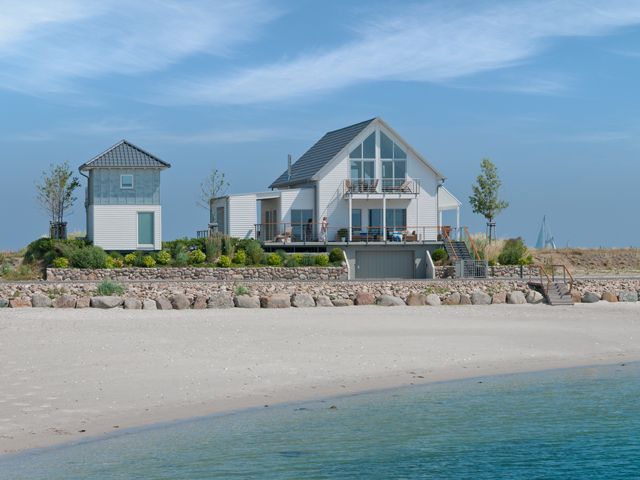
Photo: Baufritz
8. A weatherproof welded property in Australia
This family wanted ‘stillness’, which the architect at Modscape granted them with fully-welded structural steel-framed modules. Their stunning home on Phillip Island, Australia, overlooking the blustery Bass Strait, was created off-site; the modules were painted, tiled and the joinery was fitted in the company’s dedicated Melbourne factory before being delivered.
The four-bedroom house, which cost approximately £2,000 per square metre, allowed for a high level of quality control. The four-bedroom house, organised around a central kitchen/living/dining space, is designed as two simple sections; one clad in Pacific teak timber, the other in zinc.
These contrasting materials will continue to change as they weather and provide a warm counterpart to the wild coastal setting. The windows are double glazed with coastal environment-compliant anodised frames. The design also allowed for a swimming pool in an interior courtyard and a Pacific teak internal feature wall – just two aspects of the house that contribute to the feeling of nature all around.

Photo: Modscape
9. A shell home in Germany
This family home in Ludwigsfelde, Germany, is manufactured by Kampa but available in the UK from K-Haus. The panoramic glazing in the Kubos design, taking its cue from classic Bauhaus style, is orientated to the south to maximise solar gain and natural light. But this timber frame precision-engineered kit system can also be tailored to meet a range of architectural designs.
The property incorporates an off-site quality controlled closed panel system, which is delivered and erected within three to four days on a prepared foundation with windows, entrance doors and conduit for services.
It comes as a shell, shell plus (with services) or turnkey finish (with kitchens and bathrooms in situ), from £1,250 per square metre for a shell home to around £1,850 per square metre for a full turnkey option – depending on the design, fit-out and ground conditions.
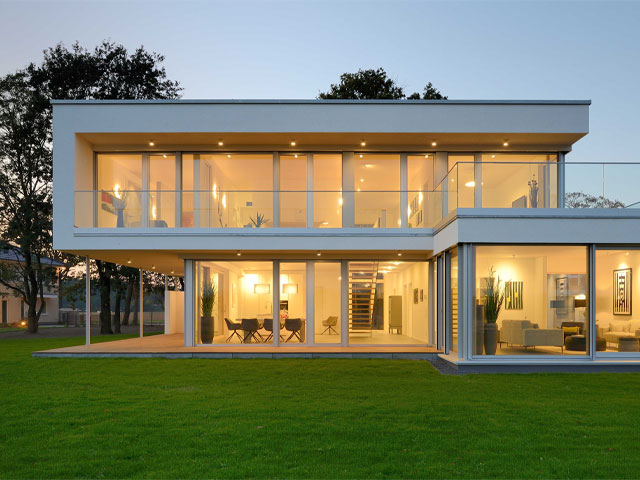
K-Haus modular home
10. A fast-build modular home in Scotland
Sutherland’s Lodge, timber-framed and with a corrugated steel roof, has the feel of a gamekeeper’s cottage. The owners say ‘it blends in with the surrounding countryside on Scotland’s west coast’ and that ‘the look wouldn’t have been possible with traditional bricks and mortar’.
The two-bedroom home was designed by The Wee House Company and built off-site complete with fitted with kitchen and bathrooms, electrical and plumbing circuits, plus the first coat of paint. It then took just three weeks to complete.
‘A plus-point of modular building is that materials are not left exposed outdoors for long but are used quickly and efficiently,’ says The Wee House Company managing director, Jennifer Higgins.
The project cost £144,573.
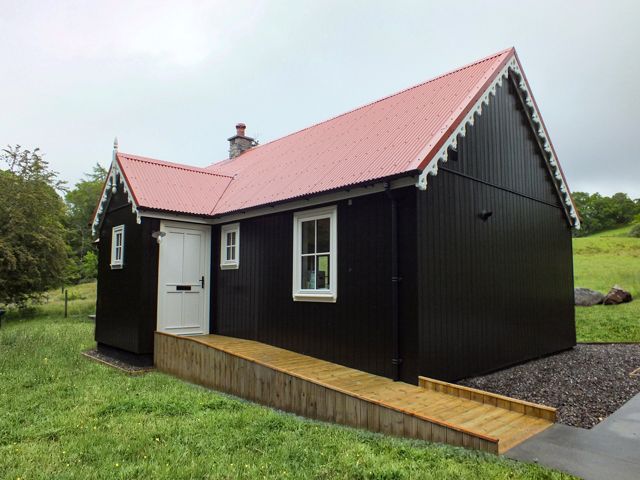
Photo: The Wee House Company
MORE ON MODULAR HOMES